Local specialists urge manufacturers not to ignore energy saving opportunities in their compressed air system
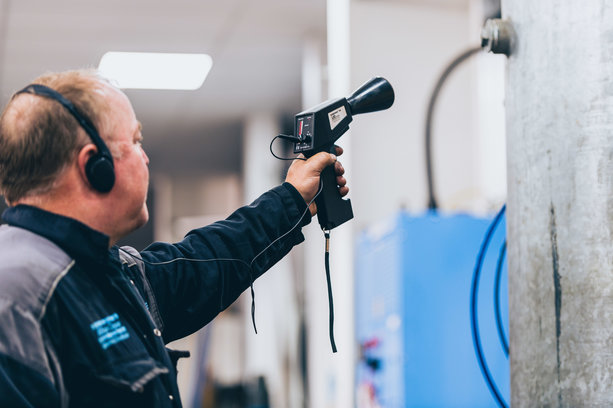
An engineer carrying out a leak detection survey
“TYPICALLY, compressed air accounts for 12% of the total energy costs for industrial manufacturers – and may be as much as 40% in some cases. For many of our customers’ compressed air is crucial to their production but it doesn’t mean it has to cost them the earth” explains Nick Forth, Branch Manager at Norman Walker.
“Locally, we have seen demand increase dramatically for our compressed air energy auditing services over the last couple of years. This has helped many businesses in the Humber region understand their compressed air energy usage but also to reduce their costs and carbon footprint”.
Norman Walker, as part of Pennine Pneumatic Services Ltd, has developed a guide to help manufacturers reduce the energy used by their compressed air system. The guide covers 10 ways to reduce energy costs.
One area to look at is fixing your air leaks. One 3mm hole in your compressed air pipework could cost you between £500-£900 a year, depending on your compressed air system and the pressure it runs at.
But, when it comes to pipework energy savings, it’s more than just fixing leaks. Things like zoning your pipework can make a big difference.
“For example, a kitchen manufacturer we work with, their full production ran on one 90kW compressor and two 55kW air compressors. While production was 7 days a week, only one process ran at the weekend. The installation of remotely controlled zoning valves meant they could run their weekend work on just one 55kW compressor. This made the system much more efficient and they are now only producing the compressed air they need,” commented Nick.
Another, energy saving tip is to lower your whole system pressure. For most compressors, a reduction of 1 bar in pressure (14.5 psi) could lead to a 7% saving in electricity consumption.
Nick explains, “Dropping the pressure in your system without affecting your production may seem unbelievable, but we can simulate changes on our software before running it on site and look at incremental changes until we find the sweet spot.”
A further consideration is switching to a variable speed drive compressor. Many industrial applications have fluctuating air demand. Using a fixed speed compressor for this results in wasted energy. A variable speed drive air compressor can deliver up to 60% energy savings compared to a fixed speed compressor.
Other areas the guide covers include making sure your equipment is correctly sized, having control systems in place, how regular servicing maintains efficiency and how you can use the energy more than once with heat recovery.
Download and read the full guide here:
www.pps.co.com/energy-saving/download-pps-guide-energy/